Safety Programs
Safe & Sound
Keep unnecessary risks out of work and know how to respond to situations.
Whether responding to an emergency or having a plan in place to stop incidents before they happen, we have policies and procedures in place that help create a campus where safety is second nature.
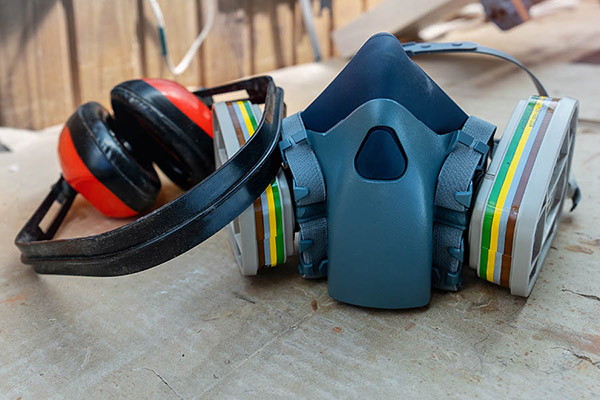
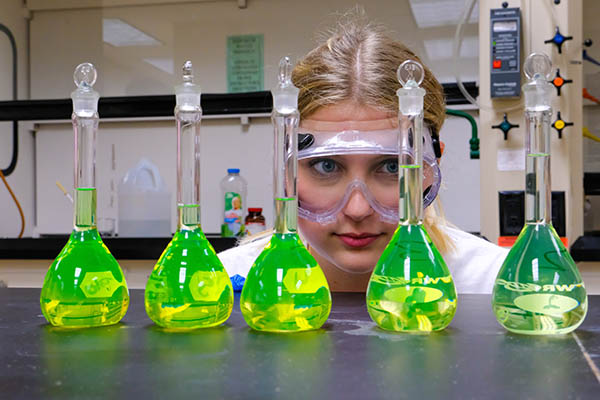
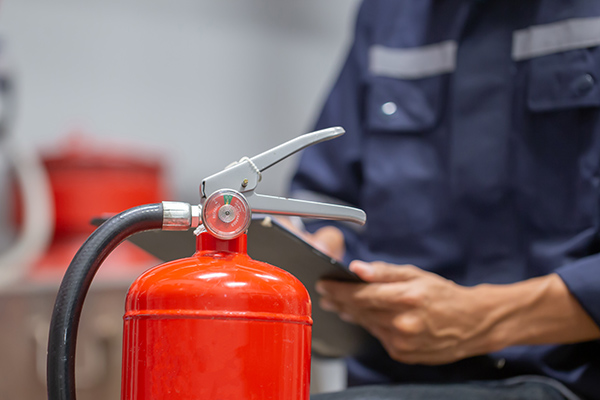
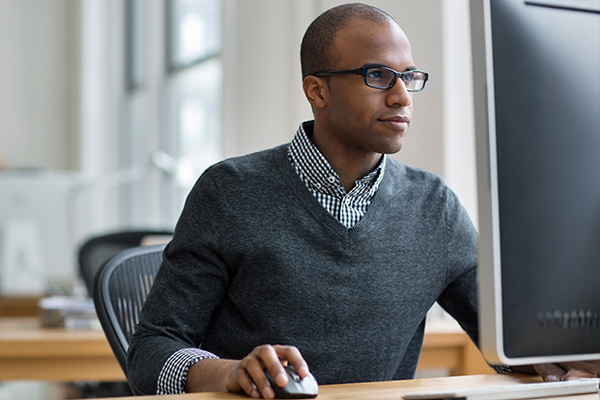
Bloodborne Pathogen Safety
Bloodborne pathogens are infectious microorganisms that can be present in and transmitted through human blood. The most common and dangerous bloodborne pathogens are hepatitis B virus (HBV), hepatitis C virus (HCV) and human immunodeficiency virus (HIV). You can become infected with one of these if you are exposed to the blood of a person who has one of these infections. Most exposures don't result in infection. However, prompt follow-up to any potential exposure is critical.
You may have been exposed to a bloodborne pathogen if blood or other potential infectious materials:
- Contact an opening in your skin (cuts, scratches, rashes, etc.)
- Contact your mucous membranes (eyes, nose, mouth)
- Have contaminated object that punctures your skin
If You're Exposed to Human Blood
If you are stuck with a needle, get blood on an open cut or in your eyes, nose or mouth or believe you have been exposed to a bloodborne pathogen, you should:
- Wash the area thoroughly
- Wash needlestick wounds or exposed cuts with soap and water
- Flush splashes to nose, mouth or eyes with large amounts of clean water
- Report the incident to your supervisor
Students, including student employees, that are exposed to human blood should report the incident to your instructor and seek follow up care with your private doctor.
If You Encounter a Blood Spill:
- Secure the area by placing signs, caution tape or a barrier to keep others away from the area.
- Call the Operations Supervisor at ext. 2241, report the location of the spill and any other information you have about the spill.
Confined Space
Confined spaces may not be specifically designed for people to work in, but they're still large enough for workers to enter and perform tasks. This policy establishes specific procedures to protect UW-Green Bay and subcontractor employees from the hazards of entry into both non-permit and permit-required confined spaces.
Ergonomics
The Environmental Health, Safety and Emergency Office can assist staff with ergonomic workstation assessments at no charge. A basic workstation self-assessment can be conducted and recommendations made to improve employee comfort while performing job tasks.
Complex Ergonomic Needs
UW-Green Bay has a contract with Prevea WorkMed to provide ergonomic services by an occupational therapist for employees who have more complex needs or pre-existing conditions. This service costs approximately $79/hour and is paid by the employee’s department.
Hazard Communication Standard
This standard requires evaluating the potential hazards of chemicals and communicating information concerning those hazards and appropriate protective measures to employees. The Hazard Communication (HazCom) Standard includes provisions for:
- Developing and maintaining a written hazard communication program for the workplace, including lists of hazardous chemicals present
- Labeling of containers of chemicals in the workplace, as well as containers of chemicals being shipped to other workplaces
- Preparation and distribution of safety data sheets (SDSs) to workers
- Development and implementation of worker training programs regarding hazards of chemicals and protective measures
All new employees at UW-Green Bay receive hazard communication training as part of the New Employee Safety Orientation they are required to complete during their first weeks of employment.
Hearing Conservation
The hearing conservation program applies to any employee whose exposure to noise is equal to, or greater than 85 dB, measured as an 8-hour TWA to prevent occupational noise-induced hearing loss for employees.
Lock Out Tag Out (LOTO)
Whenever maintenance or servicing is performed on machinery or equipment, there are minimum requirements for the lockout and tagout of energy-isolating devices. This program ensures that the machine or equipment is stopped, isolated from all potentially hazardous energy sources and locked out and tagged out before any employee performs any servicing or maintenance during which unexpected energization or start-up of the machine or equipment or release of stored energy could cause injury.
Proper Protective Equipment (PPE)
Personal protection equipment is vital to a safe working environment, so UW-Green Bay provides this equipment for employees. The use of PPE is considered when all feasible engineering controls, guards and sound manufacturing practices have been incorporated to eliminate any potential risk of injury on the job.
Respiratory Protection Program
Proper use of respirators helps protect all UW-Green Bay employees who deal with respiratory hazards. Respirators should only be used where accepted engineering controls are not feasible to limit exposure to harmful air contaminants, while engineering controls are being installed or in emergencies. All UW-Green Bay employees who use a respirator on the job are covered by program.
Silica Awareness
Crystalline Silica is a naturally occurring component in earth soils, sand, granite and many other minerals resulting in many building materials. Silicosis is a lung disease caused by inhalation of silica dust. Silica dust can cause fluid buildup and scar tissue in the lungs that cuts down the ability for the lungs to fully function. The disease is not curable but can be prevented using protective systems. This program establishes and implements a written exposure plan that identifies tasks involving silica exposure and methods used to protect employees.
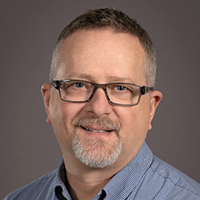
Ask an Expert
Meet Scott Piontek, Environmental Health, Safety & Emergency Manager. If you have any questions or safety concerns, he can help.